Buona parte dei bambini nati quest’anno probabilmente utilizzeranno plastiche che non uccidono l’ambiente. È sempre più forte la consapevolezza che le risorse vanno preservate, ripristinate e garantite per le future generazioni e che i rifiuti devono diventare una risorsa, anziché un problema: è la cosiddetta Economia Circolare che sta prendendo piede.
PLASTICHE DALLA CELLULOSA
In tutto il mondo si stanno mettendo a punto nuovi prodotti concepiti e progettati per essere riciclati, riutilizzati e rigenerati dopo il loro uso. In qualche caso si tratta di prodotti largamente utilizzati in passato, scalzati dal petrolio. È il caso della celluloide, creata nel 1855 dallo scienziato inglese Alexander Parkes: è una delle prime plastiche prodotte con la cellulosa, il polimero naturale più abbondante sulla Terra che conferisce rigidità e resistenza alle piante. Il materiale divenne presto la base per produrre le pellicole fotografiche e cinematografiche, ma poi fu sostituito con il sintetico acetato di cellulosa.
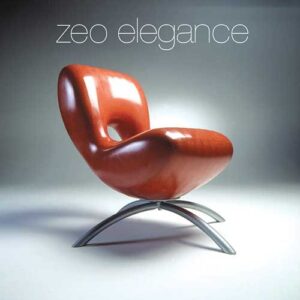
L’azienda australiana Zeoform ha sviluppato un metodo per replicare il processo naturale che si realizza nelle cellule vegetali: bioplastica fatta con acqua e cellulosa estratta da materiali recuperati e riciclati (carta, cartone, canapa, prodotti tessili, ecc.), senza colle, leganti o altri adesivi. Il risultato è una sostanza molto densa simile al legno che, essendo biodegradabile, può essere trasformata a fine ciclo in compost (una sorta di terriccio fertilizzante). Secondo i suoi scopritori potrebbe sostituire l’attuale produzione di polimeri chimici.
PELLICOLA DA INSETTI E GAMBERI
Le cuticole degli insetti in generale e il guscio del gambero in particolare, sono costituite da strati di chitina e

da proteine di un polimero polisaccaride (zucchero complesso). Estraendo dai gusci questo “zucchero al chitosanato” i ricercatori dell’Istituto Wyss presso l’università americana di Harvard, hanno messo a punto un film sottile e trasparente che ha una resistenza equivalente a quella dell’alluminio, pur pesando solo la metà. Anche questa nuova plastica è biodegradabile, costa poco e può essere facilmente modellata in forme complesse, sia per prodotti di consumo che per usi medicali.
Plastiche si riparano da sole
Altri nuovi materiali possono aiutare a superare l’usa e getta e a ridurre la proliferazione dei rifiuti e quindi lo sfruttaemnto delle risorse. Sono le “plastiche auto-riparanti”. Qualcosa che era dato per impossibile fino a poco tempo fa senza l’ausilio di calore, luce o reagenti chimici. È un po’ come avviene con le fratture delle ossa che si risaldano o con le ferite che cicatrizzano. Solo che in questo caso si usa un altro meccanismo naturale: la capacità di alcuni composti di scambiarsi gli elementi che li costituiscono per dare vita a nuovi prodotti.
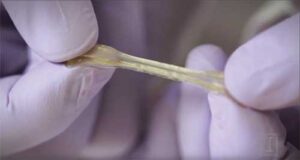
I ricercatori spagnoli del CIDETEC (Centre for Electrochemical Technologies) di San Sebastian, ad esempio, hanno usato i disolfuri aromatici derivati dallo zolfo che sono in grado di attivare naturalmente e a temperatura ambiente la riparazione di una plastica estensibile (il poliuretano); il danno viene riparato in un paio d’ore e senza l’intervento umano. Una plastica auto-riparante del genere è stata elaborata anche dai ricercatori dell’Università dell’Illinois (USA), mentre altri ricercatori americani della Case Western Reserve University hanno messo a punto un materiale fatto di un polimero che torna come nuovo quando viene posto sotto luce ultravioletta.
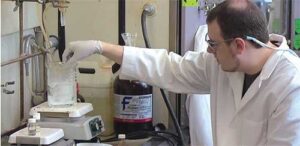
Funziona benissimo ad esempio nelle vernici. In meno di un minuto, quasi per magia, scompaiono così i graffi sui mobilie sulle carrozzerie delle auto.
Questi materiali rivoluzionari, oltre all’uso corretto delle risorse limitate del pianeta, consentiranno alle future generazioni di risparmiare anche un sacco di soldi, perché non dovranno comprare di nuovo un prodotto o un oggetto quando è stato usato e si è danneggiato. Probabilmente – grazie anche alla ricerca italiana (vedi il riquadro) – nei prossimi anni il Mondo non sarà migliore di quello attuale, ma almeno sarà un po’ più pulito.
La ricerca italiana al top
La ricerca italiana è leader nelle bioplastiche. È dell’Istituto di chimica biomolecolare del Cnr di Pozzuoli (Na) la pellicola fatta con le bucce di pomodoro poi ripresa in tutto il mondo. La bolognese Bio-On S.p.A. realizza polimeri naturali e biodegradabili (poliidrossialcanoati: PHAs) al 100% dagli scarti organici, in particolare quelli del settore agroalimentare (ad es. canna e barbabietola da zucchero).

Dunque senza dover consumare risorse in apposite piantagioni, come accade con altre bioplastiche (tipo quella delle buste).
E’ in fase di apertura di un grande stabilimento in provincia di Bologna che produrrà il materiale, in grado di sostituire le principali famiglie di plastiche tradizionali, si scioglie in acqua e in terra senza disperdere residui. Con esso si fa anche una micropolvere che ripulisce il mare inquinato da idrocarburi in due-tre settimane, lasciando zero residui inquinanti, a differenza degli attuali disperdenti. Contro le contaminazioni delle acque ci sono pure le spugne fatte coi fondi di caffè, che rendono potabile l’acqua, sviluppate dall’Istituto italiano di tecnologia di Genova, che ha inventato anche altre spugne che assorbono il petrolio, che poi si recupera spremendole. Sempre l’IIT, da gusci di cacao, arancia o crostacei, da prezzemolo, cannella, bucce di pomodoro, alghe, seta ha tirato fuori incredibili materiali plastici non inquinanti ed efficienti, persino vernici e prodotti sanitari. La Stazione Sperimentale Industria Conserve Alimentari di Parma, con piselli, lenticchie, soia, fagioli, fave, fagiolini e gusci di gamberetti rigorosamente di scarto, ha creato film biodegradabili e rivestimeni biodegradabili e commestibili per alimenti e scatolette.